China's handling of COVID has everyone talking about reshoring, and while reducing dependence on Chinese manufacturing is wise, it's not about “getting out” of China. It is about getting past the simpleminded 1990's version of globalization based on Chinese manufacturing.
Reshoring Is Neither New nor Easy
I once hosted a conference featuring the ex-President of Mexico and companies like Cisco and Disney who were working to bring their supply chains closer to customer markets. The conference tagline was “Globalization Comes Home”, and the year was 2008. Later, in 2013, Hau Lee and I published research on manufacturing strategies which found (no surprise) that global manufacturing was too dependent on China given the huge distances, long lead times and IP risks. The recommendation was to build regional supply chains closer to customers and more resilient to disruption. Reshoring is the red thread that ran through these and many similar conversations over the past 15 years.
Why so little progress since then? Maybe because China is simply too good at manufacturing and the rest of the world's addiction too deep to get out quickly. Apple, for instance is constantly in the news these days as CNBC talking heads fret over China's zero-tolerance COVID policy and the rolling lockdowns that affect iPhone supply.
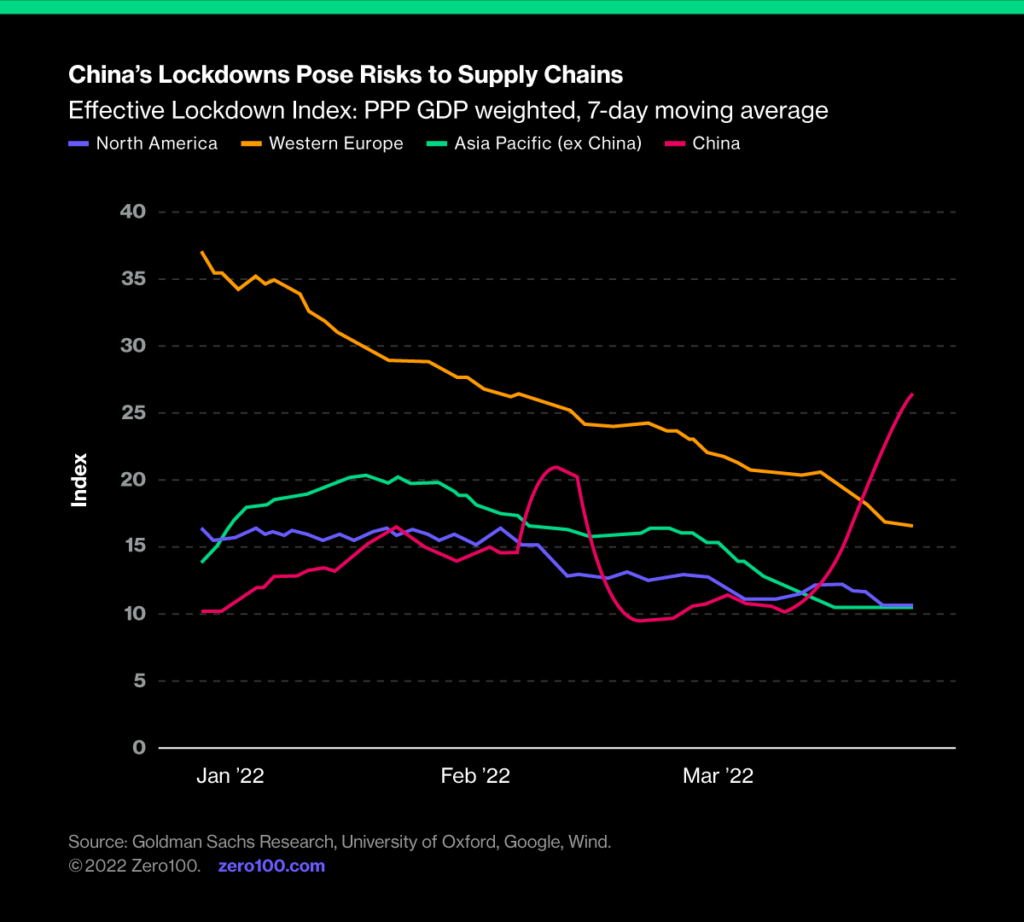
The problem is deadly serious, but does anyone really think Tim Cook needs investment managers to flag these risks? Apple's supply chain is so deeply vertically integrated that reshoring manufacturing will take many years and probably result in several similar regional hubs that are as tightly integrated as the supply chain they have built in China.
It is reminiscent of what Toyota created in the early years of its massive scale up in Japan, and probably similarly slow to export to another geography. The interconnections go deep into design-for-X philosophies, core technology, process orchestration, and human capital. This means you're not buying and assembling components so much as engineering a stack of materials, logic, and customer experience that isn't easy to render as a basic bill of materials.
In other words, reshoring isn't so simple, even if it is a good idea.
China as Customer
On the demand side of this question there is another, much less subtle reason not to decamp from China in haste – 1.4 billion customers. Dozens of big global brands we've looked at in the past three months are still, after all the political tension and COVID finger pointing, betting big on China for revenue growth in 2023 and beyond.
The legacy rules that oblige non-Chinese companies to manufacture there if they want access to the market are real, but looking forward, regionalized supply chain strategies certainly include operations in greater China. This is especially true if business wants to leverage strong brand IP, but also localize product design and retail strategies.
China as sole supplier makes business nervous, but China as customer is still irresistible.
COVID Is the Last Straw
Two megatrends have been gradually reshaping supply chain strategy for the last two decades:
Digitization of demand: e-commerce, mobile commerce, social media, and a seemingly endless array of watchdogs and influencers have exploded in the past 20 years. Supply chain digital roadmaps are trying to catch up and deliver a massive agility upgrade to handle this newly empowered customer.
Climate change: Unlike previous anxiety-inducing news cycles (population explosion, nuclear arms race, crime waves) time has not eased the worry. Uniquely, it seems to me, this trend gets worse every time they refresh the facts. Supply chain is working to tackle this because it owns Scope 3.
And yet, as powerful as these forces are, the pace of change has been glacial. Legacy systems built to manage supply chains as globalization grew following NAFTA and China's joining the WTO do the exact opposite of what digital demand and climate change require: hardwire long, just-in-time supply chains that have proven anything but resilient.
COVID, China, and the great “supply chain crisis” of the last few years may be the final straw. The world is “reshoring” manufacturing, but it is also staying in China for the long run.
We're all in this together so let's start acting like it.
Critical Reading
TECHCRUNCH
Amazon Introduces AWS Supply Chain to Help Bring Order to Supply Chain Chaos
Commentary: At re:Invent in Las Vegas, AWS CEO announced AWS Supply Chain – a cloud application that improves supply chain visibility and delivers actionable insights to help customers mitigate supply chain and lower costs.
#amazon #data
GREENBIZ
3 Primers for Buying Carbon Offsets
Commentary: Spotify and Frontier Climate are leaders among the companies standardizing and defining the process of purchasing carbon offsets.
#carbon #removal
THE WALL STREET JOURNAL
Some Retailers Are Learning to Love Bulked-Up Inventories
Commentary: Apparel, appliance, and sports equipment sellers, who are seeing resilient consumer demand in their industries, are preparing to take advantage of their excess inventories this holiday shopping season.
#demand #consumers